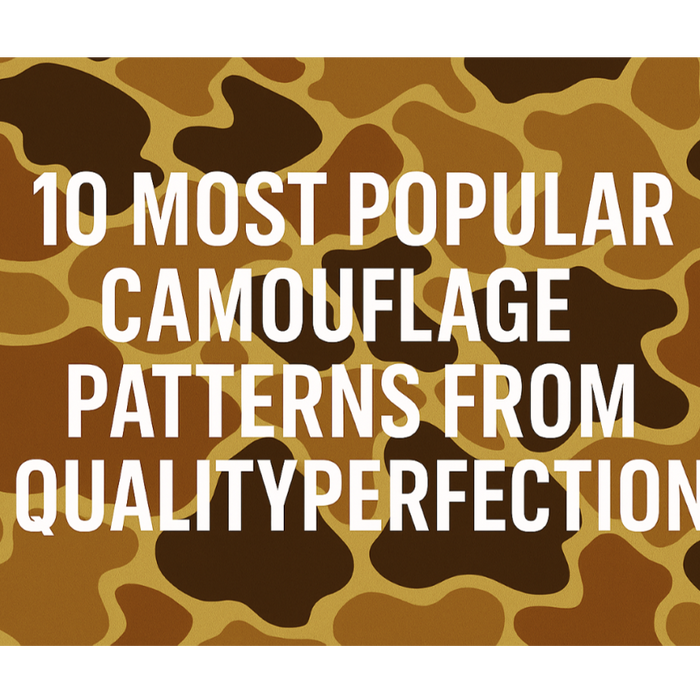
Orders 45$ & Up,
2-3 Days
Orders 45$ & Up,
2-3 Business Days
Why it’s important:
Establishing clear and measurable quality standards is the foundation of flawless product quality. Without defined benchmarks, it's impossible to evaluate performance or ensure consistency.
How to do it:
Example:
A custom koozie manufacturer might set standards for seam strength, material thickness, and print quality.
Why it’s important:
Your product can only be as good as the materials used. Compromising on raw materials often leads to defects and lower customer satisfaction.
How to do it:
Example:
Using neoprene instead of low-quality foam ensures durability and better insulation for custom drink sleeves.
Why it’s important:
Quality control ensures defects are identified and corrected before products reach customers. This prevents recalls, complaints, and damage to your brand reputation.
How to do it:
Example:
Conduct a final inspection of every batch of custom koozies to ensure print alignment and material integrity meet the established quality standards.
Why it’s important:
Your team plays a crucial role in maintaining product quality. Proper training ensures they can identify issues and take corrective actions.
How to do it:
Example:
Train production staff on recognizing printing errors, improper stitching, or material defects.
Why it’s important:
Customer feedback is a valuable source of information for improving product quality. Real-world use may reveal issues that internal testing missed.
How to do it:
Example:
If customers report that a koozie’s seams come apart after frequent washing, adjust production methods or switch to stronger adhesives.
Achieving flawless product quality requires continuous effort, attention to detail, and a focus on improvement. By following these five steps, businesses can consistently meet customer expectations and maintain a competitive edge.
Pro Tip: Regular audits and embracing new quality management technologies can further refine and optimize your processes.
Let me know if you want this as a blog post, a presentation, or an infographic!
Typically ships out in 24 hours 2-3 days shipping time (free shipping) Product Details Premium 4mm Collapsible Slim Can Koozies Holds Most Slim...
View full detailsTypically ships out in 24 hours 2-3 days shipping time (free shipping) Description: Enjoy a cold beer, a spiked seltzer, or your favorite Beer D...
View full detailsTypically ships out in 24 hours 2-3 days shipping time (free shipping) Product Details FREE SHIPPING on this item over $45 Premium 4mm Collapsi...
View full detailsTypically ships out in 24 hours 2-3 days shipping time (free shipping) Product Details FREE SHIPPING on this item over $45 Premium 4mm Colla...
View full detailsTypically ships out in 24 hours 2-3 days shipping time (free shipping) Product Details Premium 4mm Collapsible Slim Can Koozies Holds Most Sl...
View full detailsEnjoy a cold beer, a spiked seltzer, or your favorite Beer Drink flavor while keeping it cold, crisp, and delicious with a QualityPerfection can co...
View full detailsTypically ships out in 24 hours 2-3 days shipping time (free shipping) Product Details Premium 4mm Collapsible Slim Can Koozies Holds Most Slim...
View full detailsTypically ships out in 24 hours 2-3 days shipping time (free shipping) Product Details Premium 4mm Collapsible Slim Can Koozies Holds Most S...
View full detailsSamples - Might be with colors defects or print, We choose them randomly. Neoprene and foam are not the same shades of colors. The price is for 100...
View full details3 Magnets Slim can cooler sleeves FREE SHIPPING on this item over $45 Premium 4mm Collapsible Slim Can Coolers Holds Most Slim 12 oz. Cans Col...
View full details
Leave a comment